Sommaire
0. TL;TR
0.1 Contexte
Cette dépêche est la traduction d’un article paru dans HardwareX en CC-BY écrit par Vincent Martin, Jean-François Witz, Frédéric Gillon, Denis Najjar, Philippe Quaegebeur, Abdelkader Benabou, Michel Hecquet, Emmanuel Berté, François Lesaffre, Matthieu Meersdam et Delphine Auzene, présentant la mise au point d’une machine d’impression 3D métallique (utilisable aussi pour les céramiques et beaucoup de polymères). Ce travail se place dans le cadre d’une recherche reproductible et accessible au plus grand nombre. Il est à noter que c’est grâce à la licence de cet article que cette dépêche est possible. Il est ici tenté de présenter une revue aussi complète que possible de la littérature sur ce sujet, un guide complet de construction de l’imprimante, mais aussi un guide de sa configuration et une évaluation préliminaire des performances mécaniques des pièces produites. La dépêche est très longue (peut être une des plus longues publiée sur ce site), mais la personne motivée pour tenter l’aventure trouvera tout ce qui est nécessaire à la création de cette machine, mais aussi son utilisation.
0.2 Résumé graphique
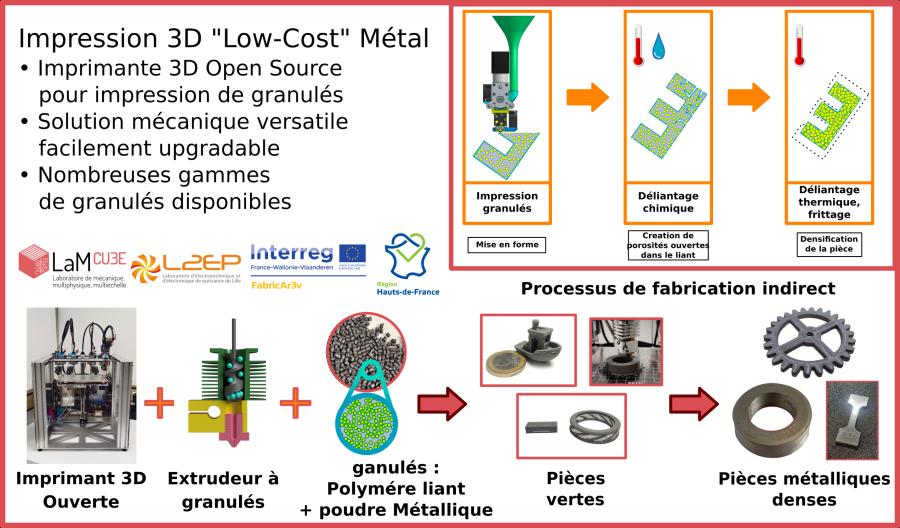
1. Le matériel dans son contexte
Les possibilités offertes par la fabrication additive profitent aujourd’hui à de nombreuses industries qui peuvent tirer parti d’une plus grande liberté de forme et d’outils standardisés. On peut citer la création de composants complets avec une seule imprimante grâce aux technologies d’impression multi-matériaux (Ayat 2020, Bandyopadhyay 2018), ou encore la fabrication de pièces plus légères aux géométries complexes pour l’industrie aérospatiale (Fasel 2020, Bhatia 2021) et automobile (Jancovics 2019, Catalucci 2016). Ces secteurs peuvent également bénéficier d’une réduction significative des coûts ainsi que d’une plus grande flexibilité dans leur chaîne de production, notamment grâce à des temps de mise en œuvre réduits et une utilisation plus économe de la matière (Singamneni 2019,Paris 2016,Dircksen 2020). Ainsi, l’application des procédés d’impression 3D aux matériaux habituellement utilisés dans ces domaines est un point de développement crucial qui fait l’objet d’une grande attention depuis plusieurs décennies (Griffith 2018), notamment pour les matériaux métalliques (Urbanek 2018, Uhlmann 2015) et céramiques (Wu 2016). Cependant, la mise en forme des métaux par des procédés de fabrication additive reste une activité très spécialisée dont les coûts d’équipement et de mise en œuvre restent très élevés (Thomas 2014, Rickenbacher 2013). Trois procédés utilisant un lit de poudre sont fréquemment employés : Le frittage sélectif par laser (SLS) (Agarwala 1995), la fusion sélective par laser (SLM) (Roehling 2019) et le jet de liant (Kumar 2017). Pour chacune d’entre elles, les différentes étapes de la mise en forme nécessitent un investissement important en équipement. Les prix couramment constatés pour une application laser se situent entre deux cents et huit cent mille euros. De plus, la mise en œuvre d’une charge sous forme de lit de poudre peut être difficile à manipuler et nécessite une forte maîtrise de l’environnement d’impression.
En revanche, l'extrusion de matériaux est une méthode abordable et largement explorée. Certaines solutions d’impression 3D de matériaux métalliques à partir d’une charge de polymère sont déjà disponibles dans le commerce. Nous pouvons citer l’exemple des systèmes d’impression MarkForged et Desktop Metal (Gonzalez-Gutierrez 2019), qui proposent de façonner des polymères chargés de poudres métalliques ou céramiques à l’aide d’un piston. On trouve également des développements de systèmes similaires dans la littérature scientifique. Volpato 2015 ont développé et étudié le comportement d’une seringue entraînée par un piston utilisé pour l’extrusion de granulés de polypropylène et Wijnen 2014 ont proposé une pompe à seringue motorisée à source ouverte qui convient aux applications d’impression 3D (Zhang 2016, Pearce 2016). Ce système a également été étudié par Li 2017 pour extruder des pâtes aqueuses chargées afin de fabriquer des matériaux céramiques de manière additive. Les auteurs ont souligné les difficultés rencontrées pour obtenir des positions de départ et d’arrêt précises des lignes extrudées en raison de la grande quantité de matière à déplacer avec le plongeur. De même, il est rapporté que la présence d’une zone inhomogène dans la matière première rendait difficile l’extrusion d’une ligne de largeur constante.
D’autres exemples utilisent également des filaments polymères remplis de poudres métalliques ou céramiques destinés à être imprimés à l’aide d’une imprimante conventionnelle Fused Filament Fabrication (FFF). On peut citer l’Ultrafuse 316L produite par BASF (Sargini 2021), ou le filament d’alumine produit par Zetamix. Cependant, peu de matériaux sont actuellement disponibles pour ce procédé, principalement en raison des difficultés rencontrées lors de la création d’un filament fortement chargé en poudre (Woern 2018) et lors de sa manipulation. En effet, la présence de grains de matière provenant d’une nature différente de celle du liant polymère fragilise fortement le matériau, notamment pour des taux de remplissage élevés. De plus, le coût de développement d’un nouveau filament rempli d’un matériau en poudre différent peut varier de cinq mille à plusieurs dizaines de milliers d’euros.
Une solution pour surmonter les difficultés susmentionnées consiste à utiliser un procédé proche du FFF, mais pour lequel la matière première est utilisée sous forme de granulés. De cette façon, la fragilité du matériau composite (liant polymère + poudre métallique) n’est plus un problème. De plus, cela permet de bénéficier des outils et de l’expérience de la grande communauté qui utilise l’impression 3D depuis près de 20 ans. Plusieurs machines employant cette technique sont disponibles dans le commerce. La société Pollen propose à la vente une gamme d’imprimantes qui utilisent ce procédé. Baptisée PAM (Pellet Additive Manufacturing), elle propose un large choix de matériaux polymères composites et son coût débute à 65 000💲. L'entreprise Eipere3D a aussi développé une imprimante 3D granulés MIM, avec un procédé de bulle chaude permettant d’éviter de chauffer l’enceinte de l’imprimante. D’autres solutions, plus orientées vers les applications industrielles, existent également comme les imprimantes ATLAS de Titan robotics, autour de 250 000💲. On peut également citer le système BAAM (Duty 2017) développé par Cincinnati Incorporated et les Oak Ridge National Laboratories ainsi que les solutions d’extrusion montées sur bras robotisé de la société Weber, qui sont destinées à la fabrication additive grand format. En effet, l’utilisation de granulés facilite le stockage et l’approvisionnement de la matière première tout en permettant un débit plus important (Moreno 2020). Cela permet de réaliser des volumes de construction plus importants comme l’illustre également l’imprimante Delta WASP 3MT dont le prix est de 49 000💲. D’autres modèles de bureau peuvent être trouvés pour des budgets plus faibles comme la BigFoot 200 de Tumaker pour 6 000💲. Un autre exemple est la société Direct3D, qui produit une tête d’impression pour l’extrusion de matériaux à partir de granulés. Enfin, il est possible d’acquérir uniquement une extrudeuse et de l’adapter sur un système cinématique à trois axes. La société Dyze Design vend l’extrudeur pulsar pour un peu plus de 10 000💲. Celle-ci dispose d’un important débit d’extrusion de matière et la température le long de sa vis peut être réglée grâce à trois zones de chaleur. Cependant, ces machines restent chères et les coûts d’investissement associés représentent une restriction importante pour un particulier ou une petite structure qui souhaiterait acquérir un tel équipement. Leur fonctionnement est fortement lié à la marque du fabricant car elles présentent souvent d’importantes restrictions logicielles et matérielles qui ne laissent pas beaucoup d’autonomie à l’utilisateur. Par conséquent, ces procédés ne sont pas bien adaptés aux travaux de développement ou à la recherche universitaire proprement dite, qui nécessitent souvent des modifications de l’équipement ou de la chaîne de contrôle. Cependant, des solutions plus simples et plus abordables, qui ne prévoient que l’extrudeuse de granulés, existent également. On peut citer l’exemple de la Bravo Basic de Polylab, une tête d’impression vendue 2 400💲, ou du Lily Kit de Recycl3dprint qui propose d’assembler un système d’extrusion similaire pour environ mille dollars. Enfin, l'extrudeuse de granulés Mahor, est disponible pour environ 500 €. Cette dernière est la solution utilisée dans ce travail pour mettre en place le processus d’extrusion du matériau.
En outre, ces systèmes ont été largement étudiés dans la littérature. Différents travaux de recherche ont mis en œuvre leur propre version d’une extrudeuse de granulés pour l’impression 3D, également connue sous le nom de Fused Granular Fabrication (FGF) ou Fused Pellet Fabrication (FPF). Une tête à alimentation multiple a été construite par Zhou 2018 pour l’impression de matériaux thermosensibles, ce qui permet de réduire la dégradation thermique subie par le polymère lors de divers traitements thermiques. Des développements similaires ont été réalisés pour imprimer différents types de polymères en utilisant une extrudeuse personnalisée (Whyman 2018, Reddy 2007). Différents points d’intérêt sont étudiés tels que le comportement physique des matériaux (souvent nécessaire pour obtenir les bons paramètres d’impression), les performances mécaniques des structures imprimées ou les mécanismes en jeu dans la cohésion entre lignes et entre couches. De même, d’autres travaux présentent la modélisation des phénomènes physiques qui régissent le transport et la fusion des granulés (La Gala 2020) ainsi que la qualité d’extrusion du matériau (Wang 2016, Rane 2019). Ces points sont essentiels pour la mise au point du procédé et le développement de cette technologie. Une autre application de la fabrication additive par extrusion de matériaux consiste à réutiliser les déchets plastiques comme matière première. Plusieurs travaux ont été réalisés sur ce thème et différents aspects ont été étudiés, tels que la faisabilité par rapport à la taille des particules et au type de polymère, les performances mécaniques ou l’impact économique du procédé sur le prix des pièces (Woern 2018,Byard 2019,Reich 2019,Dertinger 2020). La machine utilisée dans ces travaux était une Gigabot X, une imprimante 3D open-source de milieu de gamme qui peut imprimer à partir d’une matière première granulaire grâce à une tête d’extrusion thermoplastique miniaturisée qui présente également trois zones thermiques distinctes. Comme mentionné précédemment, une autre application importante de l’impression à partir de granulés est l’extrusion et la mise en forme de polymères remplis d’une poudre d’un matériau différent. Cela permet tout d’abord d’introduire une fonctionnalité supplémentaire aux pièces. Divers exemples peuvent être trouvés dans la littérature, comme les travaux de Huber 2017 ou Li 2016a, Li 2016b qui utilisent respectivement un filament chargé et des pastilles pour fabriquer de manière additive un polymère chargé de particules de néodyme. Cela leur permet d’obtenir des aimants aux formes complexes qui présentent une distribution de champ magnétique spécifique. Enfin, ce type de matière première peut être utilisé pour produire des pièces métalliques denses par un procédé appelé fabrication additive de type MIM. Pour cela, la pièce imprimée va subir des traitements thermiques afin d’éliminer le liant polymère et de solidifier les particules métalliques. Ces étapes sont similaires à celles utilisées dans les technologies de moulage par injection de métal (MIM, ou plus généralement PIM pour Powder Injection Molding (Gülsoy 2016)). Plusieurs travaux de recherche ont porté sur cette technique pour produire des pièces en différents types de métaux tels que l’acier inoxydable AISI 630 (Annoni 2016) ou 17-4 PH (Singh 2021). Des pièces en acier inoxydable 316L ont également été construites à l’aide de ce procédé, tandis que l’étape d’impression était réalisée à l’aide d’un filament d’alimentation (Damon 2019, Wagner 2021) ou de granulés extrudés à l’aide d’un système de piston motorisé (Parenti 2019). Récemment, Hassan 2021 ont étudié l’impact des paramètres d’impression et de l’orientation sur les propriétés mécaniques, la micro-structure et le niveau de porosité de la pièce frittée. D’autres matériaux sont imprimés à l’aide de l’extrusion de matériaux, par exemple des céramiques comme l’alumine (Gonzalez-Gutierrez 2018, Bellini 2005) ou la zircone (Annoni 2016). Pour aller plus loin, une grande variété de matériaux peut être utilisée puisque cette technique permet de détourner des matières premières sous forme de granulés initialement destinés à des applications MIP. En effet, une grande partie des liants polymères utilisés sont des thermoplastiques à faible température de fusion. Cela permet d’obtenir plus simplement des matières premières composites et d’éliminer en partie la question du développement, donnant accès à une large gamme de matériaux (Gonzalez-Gutierrez 2018, Grida 2003, Bernardo 2012) qui peuvent être fabriqués de manière additive et se densifier grâce à un traitement thermique.
Compte tenu de l’état actuel de l’art, il semble pertinent de proposer une solution d’impression granulaire abordable et efficace pour soutenir les développements futurs, notamment en ce qui concerne l’impression métallique de type PIM. Dans ce travail, la mise en œuvre d’une solution à faible coût pour la fabrication additive métallique utilisant la fabrication granulaire fondue à partir d’une matière première sous forme de granulés est présentée. Tous les composants nécessaires, les pièces d’adaptation ainsi que le paramétrage et le contrôle de l’ensemble sont détaillés. Afin d’illustrer le fonctionnement du système d’impression proposé, des pièces vertes sont produites à partir de granulés de polymère en acier inoxydable 316L (SS) vendus par la société PolyMIM.
Le choix de la base mécanique et du système logiciel a été fait afin de suivre l’approche Open Source Hardware (OSH). Cette initiative OSH, basée sur des composants de systèmes modulaires et facilement reproductibles, est fortement liée aux premières technologies de fabrication additive et anime encore une grande partie des projets qui y sont liés. De nombreux exemples peuvent être trouvés au sein de la communauté Maker et du projet Reprap (Skrzypczak 2020). Les solutions techniques conçues selon ces principes sont particulièrement utiles pour les activités de recherche universitaire (Pearce 2016) et pour toute structure nécessitant des systèmes avancés polyvalents pouvant être modifiés de manière extensive (Dine 2021,Bessler 2019,Ching 2021). De bons exemples de conceptions open source appliquées à l’impression 3D de métaux peuvent être trouvés dans les travaux récents réalisés sur la fabrication additive à l’arc électrique (WAAM) (Navarro 2021,Pringle 2020,Lu 2017). Dans ce cas, un système de soudage à l’arc métallique gazeux est associé à un système CNC 3D afin de construire des pièces en déposant directement des lignes de métal fondu.
Dans notre cas, les détails et les dessins des pièces sont fournis par le fabricant ainsi que les conceptions électroniques. Les composants choisis sont à la fois peu coûteux (surtout si on les compare à d’autres cartes de commande d’impression 3D ou à d’autres systèmes multi-outils) et de bonne facture. Le reste de la conception présentée ici tente de donner toutes les informations utiles allant des pièces CAO et du code de configuration aux conseils de mise en service et d’utilisation. L’objectif de cet article est de donner une voie et de faciliter la mise en œuvre du façonnage de granulés chargés pour un investissement inférieur à trois mille euros. Il s’adresse aux passionnés engagés, à la communauté scientifique et aux petites entreprises. L’installation et le réglage de la machine nécessitent néanmoins un temps de développement important. L’objectif de ce guide est d’aider l’utilisateur à aller plus vite dans les étapes de montage et de réglage afin d’obtenir une machine fonctionnelle dans un temps de mise en route que nous estimons à environ 200 heures.
1.1 Principe
Le procédé FFF est l’un des premiers procédés de fabrication additive mis au point (Crump 1992). Il fonctionne en insérant une matière première solide dans une tête d’impression mobile, qui fait fondre le matériau et le dépose sous forme de liquide visqueux. Le mouvement de la tête, synchronisé avec le flux de matière extrudée, permet de construire la géométrie de la pièce. Pour ce faire, l’objet est décomposé en plusieurs couches horizontales qui sont créées successivement. Chaque couche est formée par un motif complexe le long duquel sont extrudés les filaments de matière. Les filaments, encore chauds, se lient entre eux et avec la couche déjà imprimée pendant le processus d’application, assurant ainsi la cohésion de la pièce. Le matériau peut également être refroidi dès sa sortie de la buse pour le solidifier plus rapidement et figer la forme obtenue.
La méthode classique d’alimentation de la tête d’extrusion en matériau consiste à utiliser un filament solide stocké sous forme de bobine. De cette façon, le fil polymère est entraîné en le pinçant entre un rouleau et une roue dentée, dont la position est contrôlée par un moteur. Cependant, le bon fonctionnement de ce procédé dépend fortement de la qualité du filament. Son diamètre doit être connu et varier le moins possible pour assurer un bon contrôle du flux. La plupart des fils de 1,75 mm de diamètre ont une tolérance de 50 μm. Le filament doit également être facile à manipuler afin d’être acheminé vers le corps d’extrusion et doit être suffisamment souple pour pouvoir être enroulé. Les matériaux les plus courants sur le marché sont les polymères à point de fusion relativement bas (entre 200 et 300°C), qui peuvent être préparés sous forme de bobine de filament en raison de leur comportement élastique.
Pour mettre en œuvre l’impression 3D par extrusion de matériaux chargés, on procède à l’ajout de particules métalliques ou céramiques dans une matrice polymère mais, comme mentionné ci-dessus, ce mélange peut difficilement être utilisé comme filament. Afin de pouvoir utiliser cette formulation (polymères et poudres métalliques) sous forme de petits granulés, une adaptation de la tête d’extrusion est nécessaire. En particulier pour les éléments de chauffage et d’alimentation des granulés.
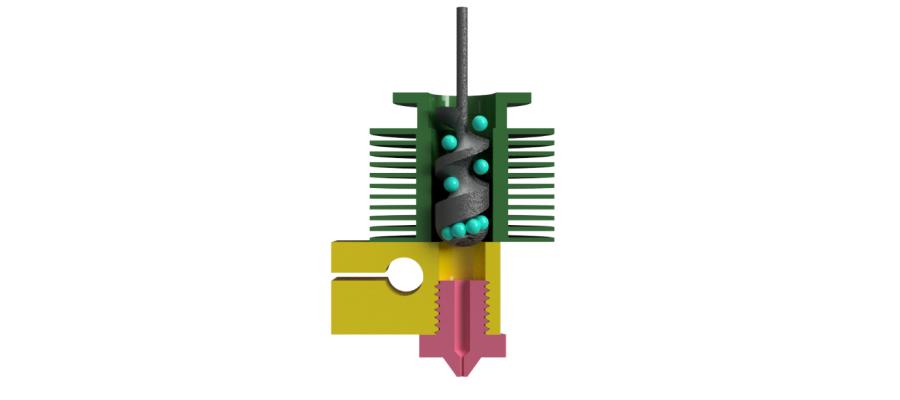
Figure 1 : vue schématique de l’extrudeuse de granulés.
La structure utilisée est composée de quatre éléments qui sont présentés par le schéma de la Figure 1.
Comme pour le procédé FFF classique, on retrouve une unité de chauffage (en jaune) et une buse d’extrusion (en rose), qui permettent respectivement la fusion et l’extrusion d’une tige de mélange polymère + charge à un diamètre donné.
Le matériau est entraîné par une vis d’extrusion d’Archimède (en gris), qui permet le transport des granulés. C’est la vitesse de rotation de cet élément et l’augmentation implicite de la pression de la matière visqueuse qui dictent le débit de la matière extrudée. Enfin, un échangeur de chaleur et un tuyau de transport (en vert) assurent la dissipation de la chaleur pour éviter la fusion prématurée des granulés à l’entrée de la vis d’extrusion et la formation d’un bouchon.
1.2 Cycle de création d’une pièce
L'objectif du processus complet est de façonner des pièces aux géométries complexes dans un matériau de nature métallique ou céramique. Après post-traitement thermique, la pièce finale sera composée uniquement du matériau cible et ne contiendra aucun polymère.
L’impression est donc la première étape, qui permet de passer des granulés à la partie « verte » (ce terme désigne l’objet imprimé constitué d’un mélange du matériau cible sous forme de poudres encapsulées dans la matrice polymère). Ensuite, une partie du liant polymère doit être éliminée lors de la deuxième étape de déliantage chimique. On obtient ainsi la partie « brune ». Ce traitement vise à solubiliser une partie de la matrice polymère afin de créer un réseau de porosités ouvertes, ce qui permet l’évacuation du reste du polymère sous forme de gaz (Setasuwon 2008) lors de la troisième et dernière étape : le déliantage thermique et le frittage. En effectuant une lente montée en température, le reste du polymère liant présent dans la partie brune est détruit. Cette étape est accélérée grâce au déliantage chimique précédent, surtout pour les pièces plus épaisses.
Enfin, la dernière étape du traitement thermique permet de réunir les grains de poudre afin de densifier la pièce par frittage à haute température. Le cycle complet est illustré dans la figure 2.
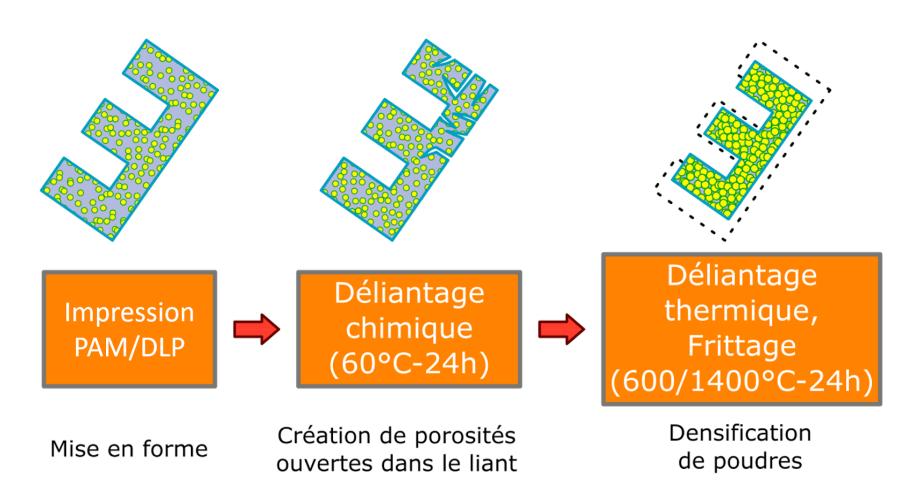
Figure 2 : processus complet pour la fabrication additive d’objets métalliques à partir de granulés.
À la fin de ce cycle, la pièce obtenue est purement métallique (ou céramique si une autre poudre est utilisée). La densité et l’état de porosité dépendent principalement de l’étape de frittage (température atteinte, durée des étapes, rampes de chauffage, contrôle de l’atmosphère) mais aussi de la qualité de la charge et de la stratégie de dépôt lors de l’impression.
2. Description
La base mécanique utilisée pour construire le système est la plateforme Tool Changer vendue par E3D (voir lien dans le tableau 2). Il s’agit d’un châssis conçu pour l’impression 3D et les applications CNC (Computer Numerical Control) qui a la particularité de pouvoir utiliser différents outils avec un seul assemblage cinématique. Pour cela, un porte-outil se déplace dans le plan horizontal et peut prendre différents modules à quatre endroits distincts. Ces modules peuvent être utilisés tour à tour au cours d’un même travail de fabrication.
Le principal avantage de ce portique est sa grande accessibilité matérielle et logicielle. Pour sa partie électronique, il utilise une carte de contrôle open source (Duet 3D) dont les paramètres et les codes sources sont tous accessibles et modifiables. De plus, le firmware de cette carte offre à l’utilisateur un grand contrôle ainsi que tous les éléments nécessaires pour permettre le développement d’un outil non standard assez facilement.
Pour atteindre notre objectif, nous avons réservé l’un des emplacements de l’outil pour une tête d’extrusion modifiée capable d’imprimer à partir de matières premières granulaires comme présenté ci-dessus. Pour cela, nous avons choisi d’utiliser une extrudeuse disponible dans le commerce, la Pellet Extruder V3 fabriquée par Mahor.XYZ (voir le lien dans le tableau 2).
2.1 L’imprimante E3D Tool Changer
L’imprimante Tool Changer, illustrée à la Figure 3, comporte quatre têtes d’extrusion FFF similaires dans sa configuration par défaut, ce qui permet une impression multi-matériaux à partir de quatre bobines de filament. Cependant, cette machine est également destinée à réunir différents processus pour offrir une méthode de fabrication hybride additive et soustractive. Par exemple, en utilisant l’impression 3D et l’usinage CNC pour une même pièce. Pour cela, les têtes d’impression peuvent être remplacées par différents outils qui devront être adaptés au châssis et au système de support des outils. En outre, toutes les informations concernant les spécifications des composants sont fournies par le fabricant. Ainsi, en plus d’être un ensemble mécanique très robuste, cette plateforme est bien adaptée au développement d’un outil dédié à l’impression granulaire.
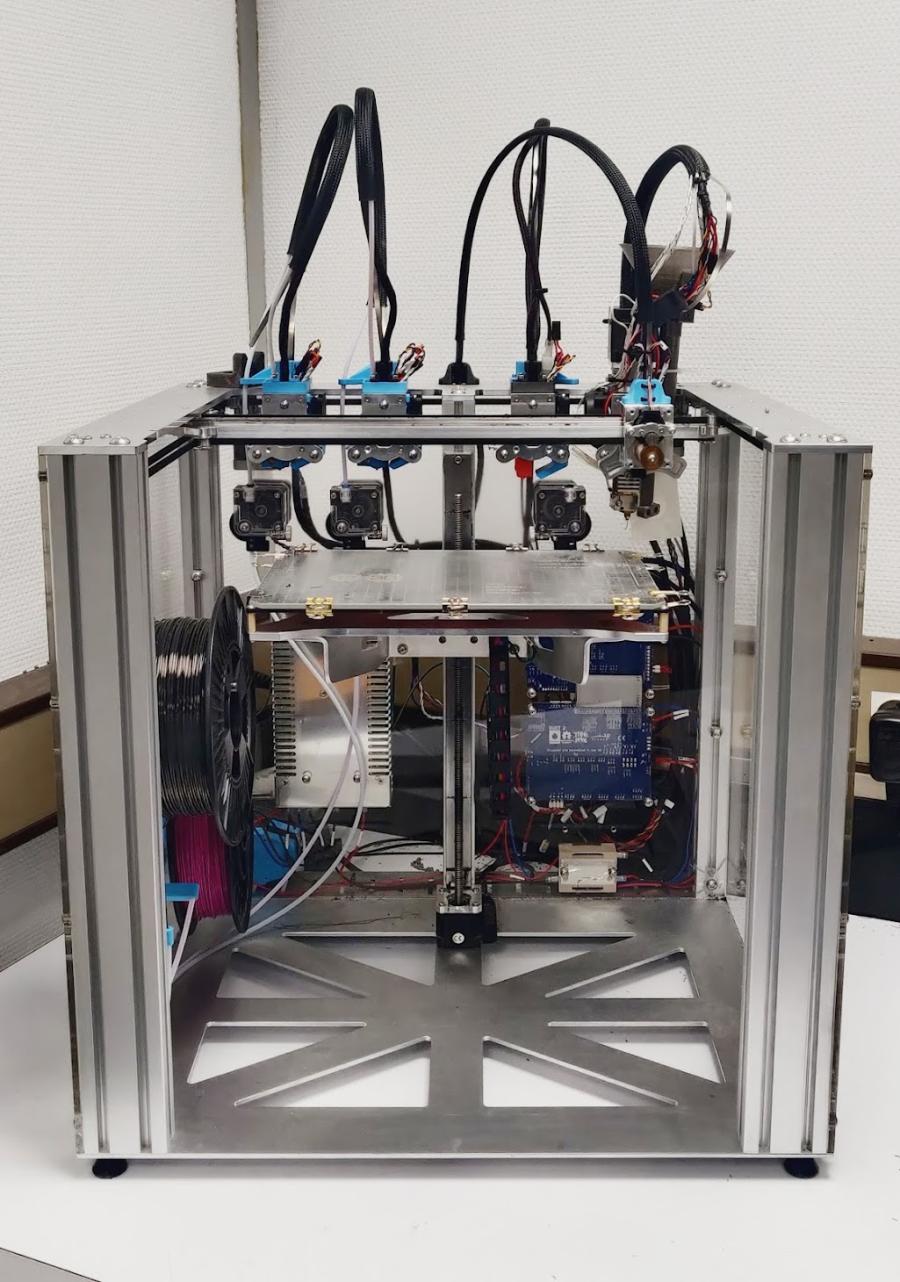
Figure 3 : imprimante E3D Tool Changer
Pour continuer, la machine est équipée d’une plaque chauffante en verre capable d’atteindre une température de 200°C et qui se déplace le long de l’axe vertical. Suivant le même principe, une chaîne cinématique « core XY » permet de relocaliser les moteurs à l’extérieur du châssis et de réduire l’inertie des parties mobiles. Cela s’avère pratique lorsqu’il s’agit d’unités d’outils plus grandes et plus lourdes.
2.2 La tête Tool-Changer
Il s’agit de la principale pièce mobile qui permet la prise des différents outils. Il est composé d’un loquet en forme de T, dont la rotation est commandée par un moteur pas à pas, et de six cylindres qui, une fois en contact avec les sphères de la plaque de fixation, forment trois liaisons mécaniques sphère-cylindre (voir figure 4.a). Cet ensemble se déplace dans le plan horizontal XY.
Le support du changeur d’outils est fait pour s’insérer dans la plaque de fixation (Figure 4.b) présente sur chaque outil et qui permet son verrouillage. Comme nous l’avons dit précédemment, cette pièce assure le positionnement de l’outil en complétant les trois connexions mécaniques, ce qui constitue un joint isostatique avec le porte-outil. Après insertion, il est maintenu en place par la rotation de 90° du loquet en forme de T à travers une fente placée en face de lui dans la plaque de fixation. C’est ce système qui permet au système de placer et de retirer les outils de manière répétée et qui garantit la précision du positionnement. Outre le dimensionnement de chaque élément en fonction de la plaque de montage, seul le poids total du module doit être pris en compte pour que le ressort de verrouillage puisse maintenir l’ensemble.
|
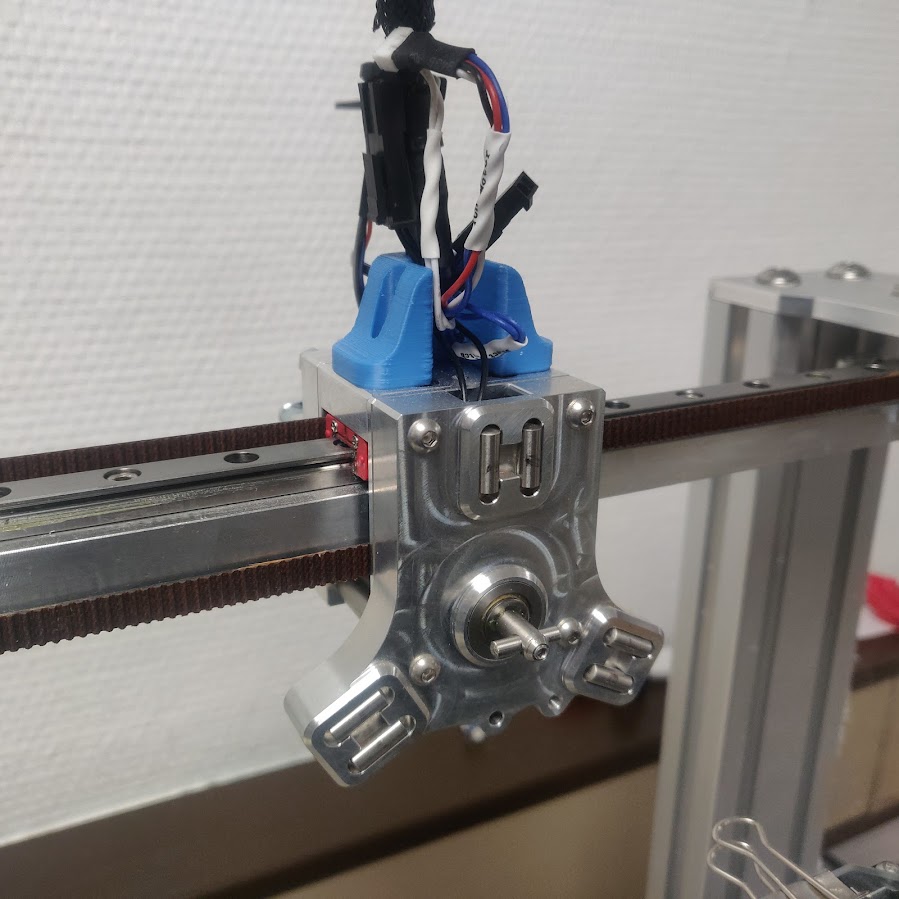 |
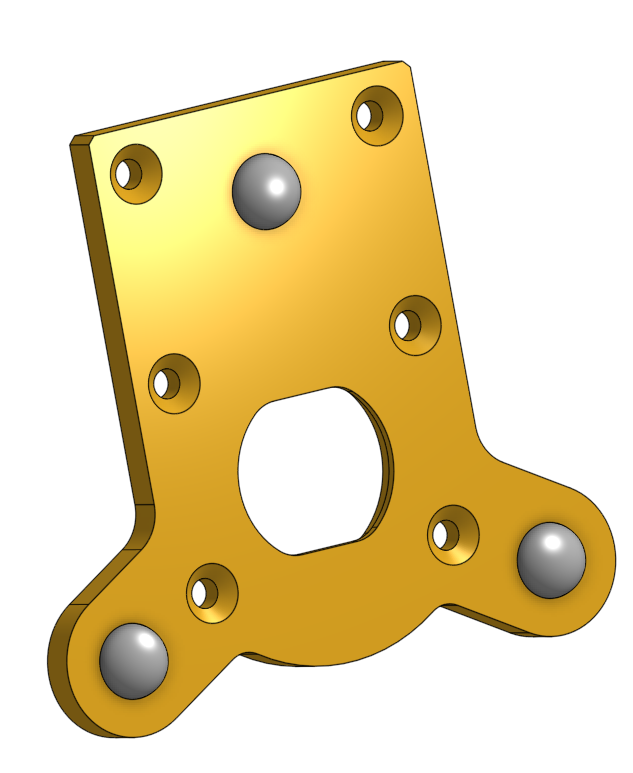 |
|
- |
a) |
b) |
- |
Figure 4 : a) porte-outil et b) plaque de montage
2.3 L’extrudeur Mahor XYZ
La tête d’extrusion Mahor XYZ V3 est utilisée pour réaliser l’impression de matériaux à partir d’une matière première sous forme de granulés. C’est un composant vendu seul par Mahor.XYZ qui se compose principalement d’une vis d’extrusion, d’un moteur pas à pas et d’une extrémité chaude (voir Figure 5). La température de l’extrudeuse est contrôlée par une cartouche chauffante, qui assure une matière première fondue suffisamment fluide au niveau de la buse d’extrusion, et par un ventilateur dont la vitesse de rotation permet de contrôler le gradient de température le long de la vis d’extrusion. La température est mesurée en deux points : directement dans la partie chaude, à côté de la résistance chauffante, et au sommet du dissipateur thermique du corps de la vis, à côté de l’entrée des granulés.
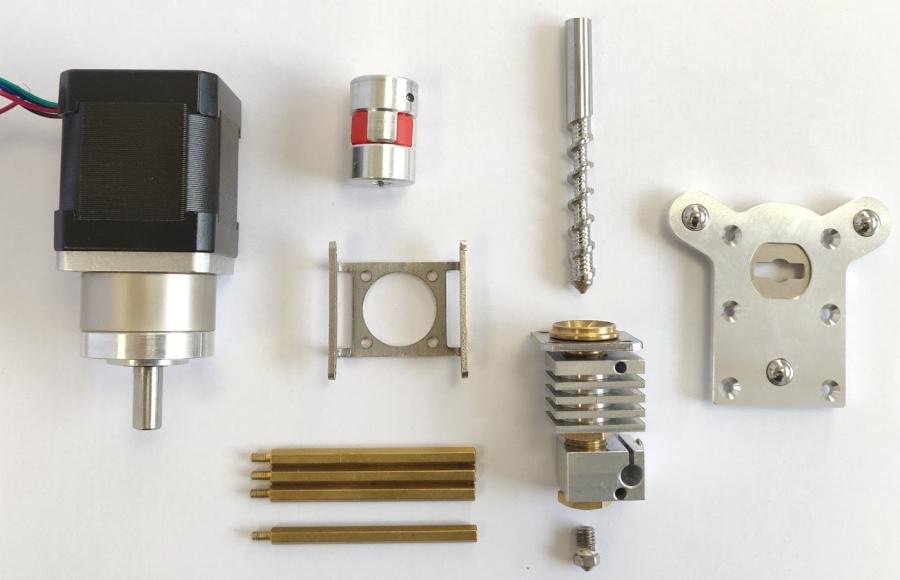
Figure 5 : pièces de l’extrudeuse Mahor V3 + plaque de fixation E3D
Une petite vis d’extrusion est utilisée pour transporter et faire fondre les granulés. Au-dessus d’elle, un réservoir doté d’un ventilateur supplémentaire permet de stocker les granulés et de les maintenir au frais jusqu’à leur livraison. Ainsi, la partie polymère des granulés reste solide pour qu’ils puissent tomber et atteindre l’entrée de la vis. La chaleur de l’élément chauffant est transférée par conduction au boîtier de la vis et à la buse d’extrusion. En ajustant correctement la température, la partie polymère des granulés est progressivement fondue pendant le processus de transport et de compression créé par la rotation de la vis.
Des pièces d’adaptation doivent être fabriquées pour adapter cet outil à la plaque de fixation présentée précédemment. Ces pièces seront présentées plus loin dans le chapitre « instructions de construction ».
2.3.1 Vis d’extrusion
Les vis d’extrusion, également appelées vis d’Archimède, sont largement utilisées dans les applications de polymères thermoplastiques. Par exemple, c’est l’outil principal pour créer de grandes formulations à partir de mélanges de polymères de différentes natures. Comme indiqué précédemment, les applications de MIP utilisent également ce processus d’extrusion afin de façonner des pièces dans un moule à partir d’une charge de granulés. Le système du Mahor V3 fait simplement la même chose dans un facteur de forme plus petit, sauf que le jonc extrudé n’est pas injecté mais déposé de manière ordonnée pour créer une forme.
La forme de la vis d’extrusion et son enceinte sont conçues pour améliorer le transport et le contrôle du flux de matière (Vergnes 2002, Hinrichs 1970). Elle est composée de trois sections : la zone d’alimentation, la transition et la zone de dosage.
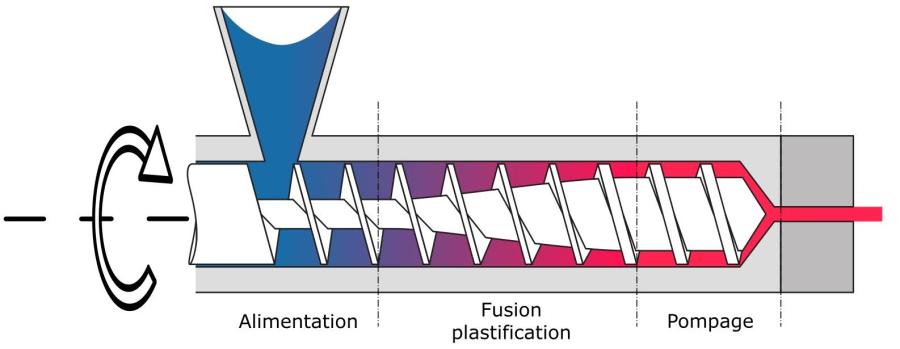
Figure 6 : conception typique de la vis d’extrusion
Le profil de la vis présente une réduction du volume disponible dans la section de transition. Cette forme crée une augmentation de la pression et permet ainsi d’écraser les granulés et d’expulser les bulles d’air.
Le résultat est un cordon de matière homogène à la sortie de la tête d’extrusion. De même, la partie d’entrée du carter de la vis présente des rayures hélicoïdales qui augmentent son facteur de friction et le transport des granulés.
Une vis d’extrusion similaire est mise en place dans le cas du système d’extrusion Mahor. La modélisation proposée par la bibliographie précédemment citée donne une relation linéaire entre le débit d’extrusion et la vitesse de rotation. Cependant, les premiers essais ont montré que le contrôle de ce flux de matière est un point critique pour obtenir une impression réussie. Des problèmes de dépôt typiques sont rencontrés lors de l’impression de petits détails où la vitesse change rapidement et où la quantité de matière extrudée est en retard sur le mouvement de l’outil d’impression. Des stratégies pour surmonter ce problème ont été implémentées dans le contrôle du code G du firmware RepRap et seront présentées dans la section des instructions d’utilisation.
2.4 Carte 3D Duet
Figure 7 : carte Duet 2 Wifi (Woern 2018)
L’imprimante E3D Tool Changer est équipée d’une carte de contrôle « Duet 2 WIFI », vendue par la société Duet3D (Figure 7). Il s’agit d’une carte open hardware et open source conçue pour contrôler les imprimantes 3D, qui a l’avantage de donner un contrôle considérable à l’utilisateur. Son grand nombre de connexions offre la possibilité de connecter plusieurs composants essentiels pour le développement de notre système d’impression de granulés. En particulier, des alimentations 24V PWM (Pulse Width Modulation) contrôlées par code G pour des ventilateurs supplémentaires ainsi qu’un second capteur de température.
La partie logicielle de la carte est assurée par le firmware (RepRap). Son principal atout est qu’il est entièrement configurable en langage G-code, ce qui permet de modifier rapidement les paramètres de la machine, alors que d’autres solutions comme Marlin nécessitent de redémarrer la carte ou de recompiler le fichier de configuration. Grâce à cela, plusieurs fonctions avancées offertes par le G-code deviennent plus flexibles et plus faciles à utiliser. Il s’agit par exemple de personnaliser le positionnement de chaque outil via des variables de décalage dédiées, ou de modifier la consigne d’extrusion à l’aide d’un multiplicateur d’avance linéaire basé sur l’accélération (« avance en pression ») ou d’une consigne de vitesse non linéaire. Le contrôle complet du code G permet également de créer des macros qui peuvent être appelées à tout moment pendant l’impression et qui automatisent des séries d’instructions prédéfinies. Par exemple, elles sont utilisées par défaut par l’imprimante Tool Changer pour effectuer la série de mouvements qui servent à la saisie d’une tête par le porte-outil ou ceux qui permettent d’améliorer l’impression de granulés. Le contrôle des imprimantes pourrait être encore amélioré avec la dernière version de la carte disponible qui pourrait inclure des capacités de courants plus élevés ainsi qu’une connectivité de bus CAN afin de s’interfacer avec une plus large gamme d’actionneurs tels que différentes extrudeuses ou outils d’usinage.
Pour résumer :
Le matériel de base utilisé ici offre un cadre très solide et ouvert, tant sur le plan mécanique que logiciel, pour développer des technologies d’impression par dépôt non conventionnelles et autres.
La polyvalence du portique de l’imprimante et la possibilité de changer d’outil permettent d’effectuer les tâches classiques de fabrication additive par extrusion de matériaux, utiles pour l’adaptation de la tête d’extrusion, tout en offrant une importante diversité de matériaux grâce à la matière première sous forme de granulés.
L’ensemble du processus de densification, hérité du procédé PIM, permet de façonner de manière additive des objets métalliques à une fraction du coût requis par les méthodes SLS ou SLM.
3 Fichiers de conception
Liste des fichiers
Tableau 1 : liste des composants imprimables nécessaires, les URLs fournies sont celles des fichiers STEP (utilisables avec FreeCAD), les sources Solidwork, ainsi que les fichiers STL directement imprimables sont disponibles ici. L’ensemble des fichiers dont les macros G-Code sont disponibles dans cette archive zip
4 Nomenclature
Désignation |
Composant |
Nombre |
Coût par unité monétaire |
Source du matériel |
Type de matériau |
Imprimante 3D |
Offre groupée ToolChanger & système de mouvement |
1 |
1854 £ |
https://e3d-online.com/products/toolchanger-motion-system-bundle |
Autre |
Imprimante 3D |
Kit de plaques d'outils et de fixation |
1 |
56 £ |
https://e3d-online.com/products/blank-tool-plate-dock-kit |
Autre |
Extrudeuse de granulés |
V3 Pellet Extruder |
1 |
500 € |
https://mahor.xyz/producto/pellet-extruder-v3/ |
Autre |
Filament d'impression 3D |
SpoolWorks Edge Filament |
1 |
25 £ |
https://e3d-online.com/collections/filament/products/spoolworks-edge-filament |
Polymer/ETG |
Vis |
M3, longueur : 8 mm, tête conique |
4 |
Inclus dans le kit d'outils E3D |
|
Métal |
Vis |
M3, longueur : 11 mm |
4 |
Inclus dans le kit Mahor.xyz |
|
Metal |
Vis |
M3, longueur : 15 mm |
5 |
26 €, boîte de 200 |
https://fr.rs-online.com/web/p/vis-a-six-pans/8229063 |
Métal |
Vis |
M3, longueur : 20 mm |
2 |
23 €, boîte de 50 |
https://fr.rs-online.com/web/p/vis-a-six-pans/0293319 |
Métal |
Vis |
M3, longueur : 10 mm |
4 |
16 €, boîte de 100 |
https://fr.rs-online.com/web/p/vis-a-six-pans/1838604 |
Métal |
Rondelles plates |
Diamètre : 12 mm |
2 |
8 €, boîte de 100 |
https://fr.rs-online.com/web/p/rondelles-plates/0189658 |
Métal |
Rondelles plates |
Diamètre : 9mm |
2 |
6 €, boîte de 100 |
https://fr.rs-online.com/web/p/rondelles-plates/0189658 |
Métal |
Ventilateurs |
40mm, 24V |
2 |
1 € |
https://winsinn.com/40mm-fan/ |
Autre |
Tableau 2 : liste des pièces requises
Après conversion, le prix total de l’investissement matériel nécessaire à la construction de cet équipement est de 2 673 €. Notez que ce montant ne comprend pas l’équipement utilisé pour le montage. Les outils nécessaires sont énumérés dans le Tableau 3.
Outils nécessaires |
Clé Allen M3 |
Petites pinces |
Fer à souder |
Fil d'étain |
Gaine thermorétractable |
Tableau 3 : outils nécessaires
5. Instructions de construction
5.1 Assemblage de la Tool Changer
L’assemblage préalable de l’imprimante Tool Changer est bien sûr nécessaire. Cette partie n’est pas abordée ici car elle est déjà très clairement présentée par l’équipe E3D, qui est à l’origine de ce système de mouvement. Toutes les informations utiles peuvent être trouvées dans une (série de documents) sur le site E3D et des instructions détaillées de montage et de configuration ont été mises en vidéo par René Jurack (Assemblage, Configuration).
5.2 Adaptation de la tête d’extrusion Mahor sur la Tool Changer
L’une des forces du Tool Changer E3D est son ouverture logicielle et matérielle. L’utilisateur reçoit des modèles géométriques au format STEP des principales pièces telles que le porte-outil et les plaques d’accouplement, ce qui facilite le travail de conception pour pouvoir adapter et monter une nouvelle tête. La version du firmware RepRap utilisée sur la carte Duet 2 WIFI permet à l’utilisateur de modifier facilement le comportement de la tête porteuse pour chaque tête. Par exemple, en spécifiant des vitesses de déplacement plus lentes pour les outils plus lourds ou en ajustant le décalage entre le porte-outil et la position de la buse de l’extrudeuse.
Dans cette section, les pièces utilisées pour monter la tête d’extrusion Mahor XYZ avec le système E3D Tool Changer sont décrites. Ces pièces sont imprimables en 3D par l’imprimante elle-même ou par toute autre solution FFF ou DLP. Ces impressions nécessitent très peu de post-traitement avant de pouvoir être assemblées.
5.2.1 Présentation des pièces
5.2.1.1 Connecteur d’amarrage en L. (« TC-Dock_L »)
Cette pièce est une adaptation du composant « TC-Dock » qui équipe les têtes d’impression à filament « bowden » (« E3D V6 ») fournies avec l’achat du changeur d’outil. Le design proposé par E3D remplit deux fonctions : il assure la liaison entre la plaque de fixation (« TC-Plate ») et le reste de la tête d’impression ou de l’outil ; il sert également de point d’ancrage pour stocker l’ensemble sur le châssis du portique une fois qu’il a été déposé par le porte-outil.